Most days, I commute on my fixed gear Diamond Back hybrid or on my Van Dessel Superfly. The Van Dessel is a great urban bike. It is equipped with a 7-speed Shimano Nexus hub. I have been very happy with the Nexus system. Its shifting cable and apparatus is inside the chainstays, which is really nice because it can't be damaged by walls, curbs, or other bikes. It looks like this:My happiness both with the Shimano and with the fixed gear bike has led to me explore a solution that encompasses the most attractive features of internally geared hubs and of fixed gears. I like having multiple gears at my disposal. I also like the simplicity of a fixed gear bike, with its lack of cables and extra "stuff" on the bike. I also like rear brakes for the winter. I ride in the snow and ice, and I think it is stupid to ride in low-traction conditions without a rear brake. I was talking with one of the guys at the bike shop (who has been commuting on a fixed gear bike since like 1965) about this, and he said that some serious commuters build up winter commuting wheels around kids bike coaster brake hubs. They like coaster brakes because there are no shifter cables to be corroded by the salt water.
So I started poking around on eBay and stumbled onto two-speed "kickback" hubs, which came standard on many kids bikes in the 70s. Kickback hubs are equipped with coaster brakes (no cables) and they can toggle between two different gears when the rider applies slight backpedal pressure. I thought I would try to build a commuter around one of these hubs. As far as I can tell, these hubs were built by two companies--Bendix and Sachs. The Bendix units came in different gearing flavors and with different brakes. According to Sheldon Brown, they are heavier than the Sachs units. Also, the cogs on the Sachs units are easily changeable, and they use the same three-peg cogs used on Shimano and Sturmey-Archer hubs. The Bendix cogs are not easily swappable. Most important to my aesthetic sensibility, however, is the the fact that the Sachs unit is Made in When it arrived, I debated with myself for a day over whether I should open it up and clean it up before committing to building a bike around it. I even emailed Sheldon Brown to ask his opinion. He graciously responded, advising me not to fix what isn't broke. I decided to act against his advice. I have taken apart automobile engines and put them back together and I was reasonably confident I could at least put this thing back together. Before opening it up, I verified that it worked by turning it by hand. In operation it is really cool. (Parenthetically, after I disassembled it, I found a German website with an exploded parts diagram for the Duomatic. I didn't really need it, but it is nice to have. This is the parts diagram. I hope I am not violating someone's copyright by reproducing it here.)
I am glad I opened it up, not only because I discovered a few problems, but also because the hub is a mechanical wonder. The machining is beautiful. It reminds me of the insides of a Porsche engine or of a Heckler and Koch rifle (don't ask how I know about that). Here is what it looked like as I started to open it up. I opened the cog side first (the side that doesn't have the coaster brake arm on it):

I slid parts onto a zip tie and took photos so that I would be able to keep track of them. I honestly don't know what most of these parts are called (in English, as least), but I kind of think I know what most of them do. The principle on which this thing operates is that it is always trying to shift gears, but forward pressure on the pedals makes it so that it can't slip into the other gear. If you apply back pressure, it allows a spiral part (called an "Antriebuchse") to turn and engage the "Bremskonus," shifting gears.
As I cleaned and disassembled, I found that a few of the bearing race surfaces were pitted. There are three roller bearings in the hub. Each roller has a cone and a ring (each of which is a race) and each has a cage with ball bearings in it. Of the three bearings, two had some pitting. The bearing on the lever arm side of the hub was in the worst shape. Both of its races were pitted and the ball bearings themselves were a bit dulled from having traveled over pitted races. My guess is that moisture got into the hub and rusted the race surfaces. On the other side, the outer race surface on the "Planetenradträger" was badly pitted. This part is seen below. It is a really neat piece of machinery. It contains three little planetary gears, held in place by three little shafts. When these planets are removed, the large bearing can come off. It is very much like field stripping an HK rifle.
Now, this method of attaching the Dremel may seem a little imprecise. It is. But that type of precision turns out not to be important for this operation. All that is really needed is a constant grind around the race. This is made possible by the rotation of the lathe and the fast rotation of the Dremel. The "float" created by the contact between the abrasive tool and the race keeps the two in a relatively constant relationship. I only took out a few thousandths of an inch, just enough to get below the bottom of the deepest pit in the race. As I understand it, the final shape of the race doesn't matter much as long as it is in certain bounds. Its main job is to have a concave surface against which to trap the ball against the concave surface of the opposing race. Far more important is the surface finish, which needs to be really nice and shiny. To get this, I risked losing a finger by polishing with emery cloth:
At first, the emery paper made a little musical note against the striations left by the grinding process. But as the striations were polished out, the process became quieter. I found that wrapping the emery cloth around the end of a wood ruler created a good tool for pushing into the races. I subsequently ground and polished the two other pitted races in a similar fashion. Here is one of the newly reground and polished races:

The races look really good--nice and shiny. I purchased two packets of new ball bearings at the local bike store and popped them into the old cages. They are 3/16" bearings. I micrometered the old and new ones because I was afraid that the hub would require metric bearings and that Wheelworks had given me English ones. The new and the old bearings were exactly (EXACTLY) .1875 inches, so they are EXACTLY right. Here are the reground races with their shiny new bearings:

One final unresolved question was whether I had ground away too much of the hardened bearing surface and exposed soft steel underneath. This would be bad because the hardened ball bearings would push into soft race material and eventually kill the race surface. I spoke with one of my friends who is possibly the world's preeminent metallurgist, and he felt that I would be fine. I ground off very little, and the material underneath is likely quite hard.

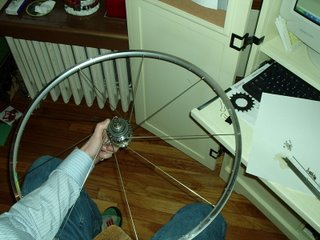
I laced up the hub with a Mavic 700c rim and DT Swiss spokes. There are 36 spokes, and I had to put tiny brass washers on the spoke heads because the Sachs steel is hard and does not "give" against the spokes the way aluminum does.

I mounted the wheel on my Redline Monocog and commuted for part of the 2005-2006 winter on the bike. It is AWESOME. I may end up selling the wheel, because I really am having a good time on the fixed gears.
10 comments:
Great post. I just picked up a Columbia Twosome equipped with a Duomatic hub. So far so good... I haven't had to rebuild it yet. If you do end up selling that wheel let me know... depending on where I am in my various bicycle projects it might have a home in my fleet. Thanks! -Chad. chad.christian@gmail.com
If you decide to sell the wheel, I want dibs! I have a Pinarello frame that could use just such a mad device, and it would make a perfect pair with my Duomatic-equipped Auto-Mini.
Mutt and Jeff!
any idea where I can get replacement axel nuts for the duomatic? I've tried everywhere, even specialty fastener shops... apparently they are somewhere in between M10 and M12 (M11?) x 1.0. Any help is appreciated. Thanks, Chad (chad.christian@gmail.com)
Great post, well explained, I would recommend covering the ways of your lathe whenever useing a toolpost grinder of any kind. Little particles of the abrasives land on the ways and are moved around by the cross slide, thus lapping the lathe bed and undoing the the initial prescision of your machine.
Some very good information in this posting. i am a big fan of the Duomatic having once owned a Moulton Stowaway in a previous life. You mentioned a German website. Do you happen to have the link?
Best regards,
Michael Downes
michaeldownesdesign@hotmail.com
Michael:
Here's the German Duomatic site.
The original exploded diagram on that site, which is also larger than DS' reprint.
Okay...this is coming in a tad late, but after nine years of having a NOS Sachs Torpedo hub in my possession, I've finally built a bike around it (pet name "FauxFix"), and, in two days of riding, I love it. The drive side is missing its protective "cover" for the bearings, but I'm hoping to find a reasonable replacement. (any ideas for a substitute?) The frame is a worn-but-loverly '84 Dawes Atlantis road frame (all Reynolds 531, lugged, etc.). Rides like a dream, and I can fully understand the new-found niche popularity for this hub ("don't know what you've got till it's gone" was seldom more true). Practically all the virtues of a fixed-gear without the hair-shirt attitude. Fixie addicts look puzzled as I come to a stop at a street light with little effort and no histrionics. Propulsion, gear shifting and braking are all controlled by one's feet – no levers or cables as intermediaries. I admit it's taking a bit of time to adjust; I haven't been aboard a coaster-brake-equipped bike, on a regular basis, anyway, in a little over forty years (I'm 51). I have several swoopy, go-fast bikes that I love dearly (including an ALex Moulton 14-speed that I bought new 22 years ago), but this may be the sweetest, sexiest practical bike I've ever owned.
If I were King, I'd decree that SRAM should put this lovely hub back into production, posthaste (perhaps with a lighter alloy shell, but otherwise unchanged). But it's probably *too* practical to see the light of day again...people like gadgets with lots of "stuff" to validate their status as consumers, so an unassuming-but-solid and sensible product gets overlooked. More's the pity.
- Barrett
The Duomatic is back:
http://hubstripping.wordpress.com/2007/11/01/the-hub-treasure/
Also details about the F&S Torpedo Automatic hub (for 20″ up to 24″ wheels) which has not the backpedal inconvenience.
Gruß Marco
Post a Comment