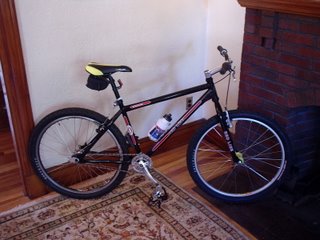
About a year ago, I bought a bare bicycle frame on craigslist. It is a Redline Monocog, a bike that was intended to be a single-speed mountain bike. This particular frame is cool because it is made of steel (some Monocogs are made from aluminum) and because the Redline letters on the frame look like a Boston Red Sox font. I built the frame up with road bike wheels, the rear having a Sachs Duomatic hub. I commuted on this for some of the winter, and it was really cool. But since then it has sat in our basement collecting dust.
A few weeks ago, I woke up in the middle of the night with the idea that it would be very cool to build this bike up as a mountain bike, and in particular as a fixed-gear mountain bike. When I get an idea in the middle of the night, I have to work on it. So I began collecting parts at local used bike stores and on eBay. Here are some of the parts:
Rear Wheel: I had a flip-flop rear road wheel I bought at Simple Living Bicycles in Framingham, Massachusetts. It was a 700c rim with a Suzue hub. Because the rim was too large for a mountain bike, I took the wheel apart by unscrewing all of the spokes nipples and removing the spokes. I bought a new (old) 26" rim at Bikes Not Bombs. It and the hub have 36 holes. I calculated the apprpriate spoke size using Spocalc, bought spokes, and built up the wheel. I use Sheldon Brown's wheelbuilding instructions when I build wheels. I ended up putting on an 18-tooth cog on the fixed side and a 16-tooth freewheel on the other side.
Front wheel: I had a 28-hole BMX hub that I had bought on eBay a few months previous. I bought a 28-hole mountain bike rim on eBay. I had hopes of building it up with a radial spoke pattern, but was a little afraid about breaking the hubs. The concern was mooted when I found that my local bike store only had spoke lengths that would allow me to build the wheel with a 3-cross spoke pattern. So that's what I did.

Cockpit: I had a stem, handlebar, and levers I bought from a kid who does freeride mountain biking. The front lever is an adjustable brake lever that can work with either v-brakes or cantilever brakes, and the rear lever is for cantilever brakes only.

Brakes: I have a box of miscellaneous parts from previous bike projects. I had a set of front v-brakes and rear cantilevers. I attached these to the frame. There was no rear cantilever cables stay on the frame, so I got (at Broadway Bicycle School) the kind that mounts via the seatpost pinch bolt. I cut brake cables and housing to fit using my Dremel cutoff wheel.
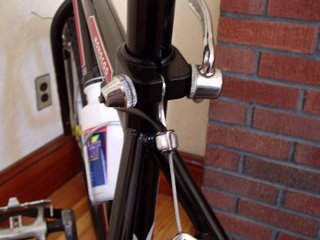
Tires: Craigslist bargain Bontrager Jones XR.
Crankset: Chainring side is a Sugino MTB crank with a 170mm crankarm. I took off the large and small chainrings and left the middle one, which has 34 teeth. I subsequently had to use the granny gear as a spacer to get the chainline right. I was looking for a 32-tooth chainring because I have a 16-tooth rear cog and most people seem to like a 2:1 ratio on fixed gear mountain bikes. But 34 was the best I could do. For the left side, I didn't have a crankarm to match the right side, but I found another 170mm crank in my pile of old parts. They don't match, but they are the same size and work just fine.

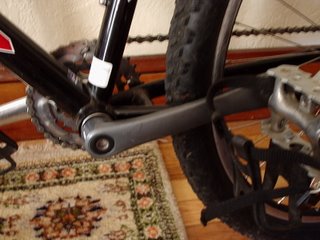
Rear Axle: The Suzue track hub had a solid rear axle, but I wanted to make it quick release so that I could easily flop the wheel over when I want to switch between the the fixed 18-tooth cog and the free 16-tooth freewheel. Track and wanna-be messenger types like to have solid axles because they are strong and because they deter casual bike wheel thieves. But my bike won't be outside unless I am sitting on it. And if you want to flip over the wheel on one of these, you have to carry a wrench with you. So I took a hollow axle from an old rear road wheel, and cut it down to size with the Dremel cutoff wheel. Its bearing cones fit the Suzue bearings. I also cut down a quick release skewer and tapped more threads on it using a 8.5 x 5 metric tap. I had some cheapo chain tensioners that were made for a bike with thicker axles, so I cut them down to fit my axles.



I went out for a ride with my friends on Saturday. They were quite skeptical about the bike and thought that they would be waiting for me a lot. We have a reasonably technical ride route, with some pretty nasty nasty descents, climbs, and lots of undulating terrain with roots and loose rocks. The bike was AWESOME! It was a blast to ride. I kept up with everyone, and found myself right on the tail of the fastest guy a number of times. Because I commute to work every day on a fixed gear, it wasn't too difficult to transition to this on dirt. It is a little odd to have to pedal over jumps and big obstacles. I did feel like I had more control on loose stuff and on steep descents. And on big ascents, I had to think ahead and get up some speed at the bottom of the hill. That's probably the right way to attack ascents, anyway.
All in all, I am very happy about this bike build. It is awesome.